KAYRAN
2017
O nosso primeiro veículo, KAYRAN, lançado com um ano de equipe. participante da edição de 2017 da competição Fórmula SAE categoria elétrico.
3 cups
Flour
80Ah
4380RPM
1½ cups
Butter
Rotação Nominal
Vel. Máxima Estimada
83km/h
48kW
Potência Máxima
Capacidade Acumulador
Autonomia
22km
45km/h
Velocidade Base
88
Células
Química da célula
LiFePO4
Navegue pela página e conheça mais do protótipo, use os botões ao lado para ir direto ao ponto, caso contrário, pode navegar e conhecer todos os sub-sistemas do carro. Ao final da página temos uma galeria com várias fotos.
SISTEMA TRATIVO
O projeto Tesla 2017 conta com dupla motorização traseira independente com utilização de diferencial eletrônico. Esta configuração possibilita um vasto estudo de projeto para aplicação em diversas situações de dinâmica veicular diferentes como provas de aceleração e provas de skidpad(aceleração lateral), além de altos níveis de controle de estabilidade do veículo.
A utilização de conversores DC/DC bidirecionais com a finalidade de diminuir a quantia de células em série no acumulador, é uma solução comum em veículos elétricos. Porém neste caso mostrou-se desnecessária devido à tensão reduzida de alimentação dos inversores: 72V nominais.
Por fim, seguem as características do sistema trativo. A velocidade máxima exata somente poderá ser obtida em processo de testes, podendo ser fornecida boa estimação de sua grandeza.
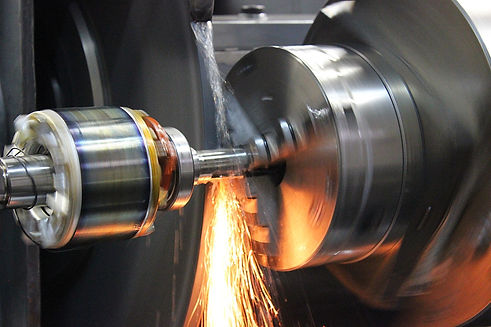
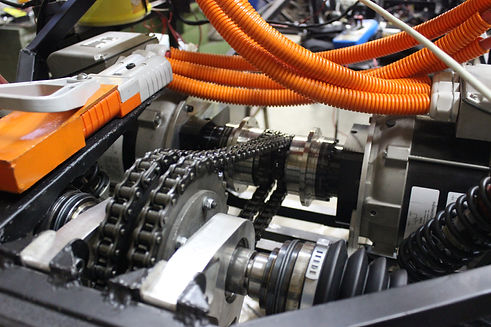
TRANSMISSÃO
O sistema de transmissão é responsável por transformar e conduzir o torque do eixo do motor à roda. Todo seu projeto e dimensionamento estão intimamente ligados às soluções de tração do veículo, a partir de sua motorização e projetada para melhor empacotamento final. Em um veículo elétrico, pode-se utilizar tanto um diferencial mecânico – para um único motor – quanto um diferencial eletrônico – para a configuração de um motor para cada roda trativa.
Optou-se, por fim, por uma redução em dois estágios. No primeiro, logo na saída de cada motor, um redutor de engrenagens planetárias da fabricante Apex, cuja razão de velocidades é de 4:1. O segundo estágio é feito por corrente (da fabricante Tsubaki), como explicitado na figura x, com razão 2,25:1 (15 dentes no pinhão e 34 na coroa). Ao final, tem-se uma redução 9:1. Esta configuração possibilitou o posicionamento desejado dos motores e um bom torque máximo, além de ser possível a troca da coroa para serem realizados testes com outras razões, de forma a validar o projeto elaborado.
ACUMULADOR
O acumulador ou banco de baterias, é o sistema responsável pelo agrupamento das células de baterias, de forma a fornecer toda a energia necessária ao sistema trativo. O projeto de 2017 conta com o banco de baterias dimensionado para que toda a prova de enduro (22km) seja completada, o ciclo de direção desta prova, na competição do Fórmula Elétrico Brasil de 2016, foi simulado em ambiente Advisor (Advanced Vehicle Simulator).
Como resultado da simulação, obteve-se que os 22km do enduro da competição representam 15MJ de energia drenados do banco de baterias. Por volta de 4,5MJ foram regenerados, o que configura em uma descarga líquida de por volta de 10,5MJ.
Assim, após estudo destes fatores e de soluções implementadas, chegou-se ao valor de 5,8kWh, que representa por volta de 20MJ, considerando descarga líquida de 13MJ. Isso possibilitou a escolha das células de lítio e de sua organização paralela ou em série, dependendo da tensão de operação do barramento CC.
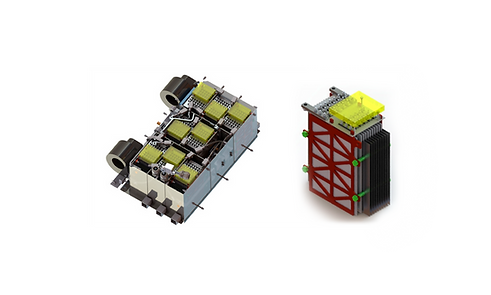

BMS
O BMS, nome que deriva do inglês Battery Management System, compõe todo o sistema de gerenciamento de baterias, responsável por garantir a utilização ótima da energia existente e reduzir os riscos de danos que às mesmas, otimizando assim sua vida útil.
O BMS é totalmente desenvolvido pela equipe. Tal escolha se deu com o objetivo de redução de custos, confiabilidade e total controle sobre o projeto. No desenvolvimento do mesmo focou-se em versatilidade e fácil manutenção. Ele foi dimensionado para servir especificamente para a competição e seguir de acordo com as necessidades do veículo atual. Outra qualidade em relação à maioria das soluções comerciais é o uso de sensores digitais em todos as medições críticas, propiciando alta qualidade dos sinais obtidos.
O design do BMS foi pensado de maneira modular, de forma que o centro de tratamento de dados se conectar a módulos de aquisição. Isso permite que esse projeto possa ser usado para monitorar bancos de baterias de uma ampla gama de tecnologias e uma vasta possibilidade de configuração de células facilmente. Com isso, ele pode ser utilizado no futuro, mesmo que o banco de baterias sofra alterações. A manutenção também se torna simples, uma vez que módulos podem ser substituídos facilmente.
Suas funções gerais são: gestão de baterias, gestão da potência e gestão de energia. Para controlar de forma efetiva o estado da bateria, o sistema deve monitorar a tensão, temperatura, o estado de carga, e a corrente. Os dados coletados resultam num banco de informações que permitem uma otimização do uso de energia do carro em projetos futuros.
Outra função importante do BMS é o balanceamento das células, para garantir que a tensão de operação pontual seja mantida em níveis seguros, garantindo uma maior vida útil para o sistema.
Além do monitoramento constante, o BMS é também responsável por possibilitar a desconexão do acumulador do sistema trativo por meio dos AIR’s, uma vez que ocorra detecção de falhas.
Tal projeto é muito crítico, por colher dados essenciais para o funcionamento do sistema global, bem como zelar para um bom uso dos acumuladores, que permanecem sem dúvida, dentre os componentes mais caros e críticos do veículo.
CONTROL SYSTEM
O controle do sistema trativo do projeto 2017 do Fórmula Tesla UFMG atua no ajuste das forças longitudinais (tração e frenagem) aplicadas nas rodas através do controle vetorial individual dos motores. Especialmente em motores de indução, caso visado pela equipe, o controle de tração tem precisão e estabilidade excelentes devido à fácil manipulação de seu torque, inclusive em sua faixa negativa (frenagem regenerativa).
O sensoriamento das variáveis do veículo dá início ao processo, considerando a velocidade individual de cada roda, o esterçamento do volante, a posição do pedal de aceleração e freio, os demais graus de liberdade na aceleração atual do veículo, entre outras grandezas relevantes. Os dados são então analisados por uma unidade de processamento central que envia os comandos de controle vetorial aos inversores.
A plataforma selecionada foi o PIC® da Microchip. Apesar dos primeiros contatos com a programação requisitarem um bom tempo para aprendizado, ela proporciona uma maior flexibilidade e controle sobre as pequenas decisões tomadas no microcontrolador.
Cabe por fim citar as extensas vantagens do controle de tração a ser implementado:
Geração ágil e precisa, que não resulta em desaceleração indesejável e perda de velocidade do veículo, em contrapartida a alguns sistemas de controle de automóveis a combustão que utilizam-se de forças de frenagem para manter a estabilidade do veículo, o que resulta em perdas de velocidade invasivas ao condutor;
Geração de momentos de guinada corretivos contínuos, visando melhorar a condução do veículo e a estabilidade instantânea, ao invés de operar somente em situações críticas de direção;
Aumento da segurança do veículo fazendo um controle de torque em curvas, evitando perda de aderência;
A efetividade do sistema independe da diferença de velocidade entre as rodas esquerda e direita;
Aumento do desempenho em acelerações, podendo operar no estado ótimo de velocidade relativa entre pneu e solo, possibilitando transferência máxima de torque.
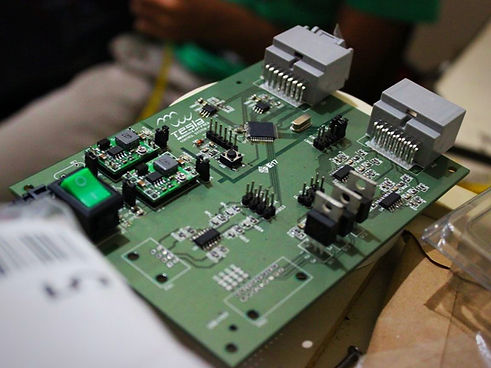

ECU
Por estabelecimento das regras da SAE, caso ocorra o acionamento do circuito de desligamento ou do botão de emergência, o sistema de tração deve cair a menos de 60V DC ou 25V AC RMS em menos de 5 segundos. Toda corrente que flui dos acumuladores deve cessar imediatamente.
Este procedimento de interrupção do funcionamento do sistema de tração pode ser iniciado por uma série de dispositivos, a saber, duas chaves mestre (Master Switch), três botões de emergência (Shutdown Button), chave de fim de curso do freio, IMD, sensor de inércia, BSPD e BMS.
O IMD é responsável por avaliar se a resistência entre os condutores de alta tensão do sistema de tração e a referência de terra, no caso o chassi, está conforme regulamentação da SAE (>500Ω/V). Este dispositivo é usado para monitorar a condição do isolamento do sistema de alimentação por corrente contínua (CC) assim como para o setor pós-inversor, que opera em corrente alternada (CA).
O sensor de inércia é um dispositivo eletromecânico que se desarma ao sofrer uma desacelerações muito acentuadas, que indiquem algum tipo de impacto. O sensor deve acionar devido a uma desaceleração na faixa de 6g a 11g, dependendo da duração desse processo.
O BSPD monitora os pedais do freio e do acelerador. No caso de ambos serem pressionados por mais de 0,5 segundos, o sistema trativo deve ser desarmado.
O ECU, como demonstrado no diagrama, agrupa os dados de todos os sistemas anteriormente citados e realiza as ações necessárias segundo cada estudo. Com isso,o ECU é classificado como essencial, pois não somente recolhe uma série de informações relevantes para dirigibilidade do veículo, possibilitando posteriores evoluções no desempenho do projeto, mas também é essencial para a segurança do piloto e do veículo.
CHASSI
A estrutura de um carro estilo fórmula deve cumprir duas funções básicas: o empacotamento de todos componentes que tornam o veículo funcional e garantir a segurança do piloto em casos de acidentes. Nesse contexto, o subsistema do chassi é responsável por, além de satisfazer essas duas premissas fundamentais, desenvolver uma estrutura com a menor massa e simultaneamente com as melhores propriedades mecânicas, ademais de prover ao veículo uma apropriada aerodinâmica e ergonomia ao piloto.
Assim sendo, deliberou-se sobre o tipo de chassi e o material a ser empregado na construção do veículo. Nesse sentido, as principais demandas consideradas na escolha do modelo de chassi foram rigidez estrutural, facilidade de fabricação e manutenção, peso e custo. Por conseguinte, a escolha lógica foi o chassi tubular, com o material sendo o aço SAE 1020, uma vez que é mais barato com relação aos outros e fácil de manusear, além de prover a habilidade de reparar, substituir ou modificar facilmente qualquer tubo.
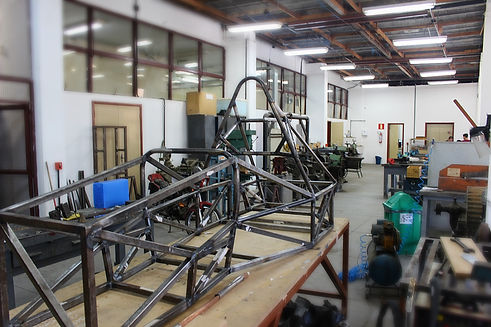

SUSPENSÃO
O sistema de suspensão do Fórmula Tesla UFMG é projetado com os seguintes objetivos:
-
Garantir e otimizar o contato dos pneus com o solo (aderência)
-
Distribuir corretamente a carga vertical entre os pneus (estabilidade)
-
Isolar a massa suspensa das irregularidades da pista (minimização das acelerações verticais)
Tendo isso em mente, foi adotado o sistema duplo-A, que tem como principal vantagem possibilitar uma infinidade de geometrias e, portanto, uma maior liberdade de projeto. Também proporciona uma ótima estabilidade ao garantir o controle preciso da roda, além de permitir vários ajustes, o que é fundamental para carros de competição.
A distância entre-eixos e a bitola foram escolhidas tendo em vista proporcionar ao veículo uma boa agilidade em curvas de pequeno raio. Além disso, conseguiu-se obter uma distribuição estática de peso de 50:50, ideal para a estabilidade em curvas.
Os amortecedores empregados são específicos para competição e, para seu acionamento, optou-se pela utilização de barras pull/pushrod associadas com balancins, objetivando um bom aproveitamento do seu curso. Na traseira adotou-se a configuração pushrod, buscando-se posicionar os amortecedores dentro do chassi, de modo a deixar caminho livre para os semi-eixos traseiros. Já na dianteira, optou-se pela configuração pullrod, visando à alocação dos amortecedores do lado externo do chassi, a fim de facilitar seu acesso.
Os cubos de roda e respectivos rolamentos utilizados são de veículo de passeio, tendo seu emprego justificado pelo baixo custo e, no caso dos rolamentos, pela presença de ímãs de sensor ABS, utilizados pela eletrônica para medição da velocidade das rodas.
As mangas de eixo são compostas por chapas soldadas, de produção relativamente simples, realizada pela própria equipe. A conexão dos leques com a manga é feita através de rótulas radiais, que são contidas no corpo dos leques formando uma única peça, possibilitando uma melhor distribuição das tensões.
A geometria adotada nos leques visa um bom controle dos movimentos da carroceria, bom controle da orientação do pneu em curvas, além de uma baixa variação de bitola em função do curso da suspensão.
Ainda é válido mencionar que a suspensão foi pensada para ser de fácil reparação, não sendo necessário desmontar nenhum outro subsistema para acessá-la e vice-versa.
DIREÇÃO
O sistema de direção tem como base 3 características fundamentais, seguindo o que é usualmente proposto no setor automobilístico. São elas: Segurança, Conforto e Semi-reversibilidade.
Seguindo esses princípios, o projeto do sistema de direção do veículo se baseia na geometria de Ackermann, que, para as baixas velocidades exigidas na competição Fórmula SAE, é altamente recomendável.
O tipo de acionamento de direção mecânica escolhido foi o pinhão-cremalheira, devido ao menor custo, a maior simplicidade, que por sua vez facilita a implementação e diminui a chance de erros, e ao menor peso que esse tipo de acionamento proporciona.
O desenvolvimento do projeto, feito principalmente no software SolidWorks®, foi realizado mantendo-se sempre uma relação direta com o subsistema da suspensão para a definição de parâmetros como câmber, cáster e KPI.
Foi analisada a relação entre o torque aplicado pelo piloto no volante e o torque aplicado pela cremalheira nas rodas, o que nos permite definir as dimensões, o passo e o número de dentes do pinhão de modo a diminuir os esforços do piloto e melhorar seu controle sobre o veículo.confiabilidade

FREIOS
O projeto 2017 de frenagem hidráulica do Fórmula Tesla UFMG, possui foco em desempenho e segurança. Para construção do sistema, toda a dinâmica deve ser levada em conta para que ocorra o travamento total das quatro rodas e estagnação segura do veículo.
Para modelagem do conjunto é necessário considerar uma larga gama de parâmetros. Determinando o torque de frenagem em cada roda a partir do modelo estabelecido, será utilizado um conjunto de componentes mecânicos e hidráulicos capazes de formar um sistema que tenha o potencial desejado. Para isto, é necessária a geração de um torque reverso em cada roda, maior ou igual ao torque de frenagem determinado.
Quando o piloto pisa no pedal do freio esta força é transmitida pelo fluido que faz com e a pinça pressione o disco, e por atrito o carro pare.
Com sistema simples, a equipe espera nos próximos anos, apresentar em conjunto com a frenagem hidráulica, uma frenagem regenerativa, colaborando para diminuição do banco de baterias.
GALERIA
![]() | ![]() | ![]() |
---|---|---|
![]() | ![]() | ![]() |
![]() | ![]() | ![]() |
![]() |